Task 5.1: Micromachining the polymer radiation dosimeter and silica optical fibre oxygen sensors
We used fsL processing for the realisation of high-resolution micromachining of polymer (Fig. 5.1.1) and silica optical fibres (Fig. 5.1.2), in the core region, at the fibre end face, forming end-face cavities.
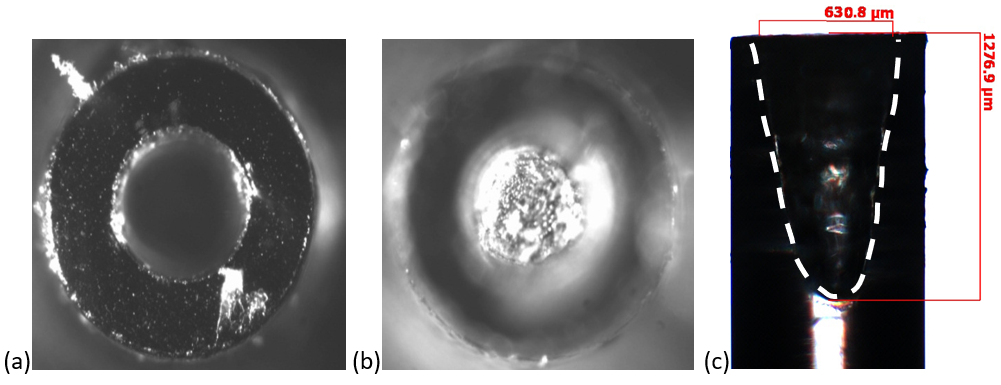
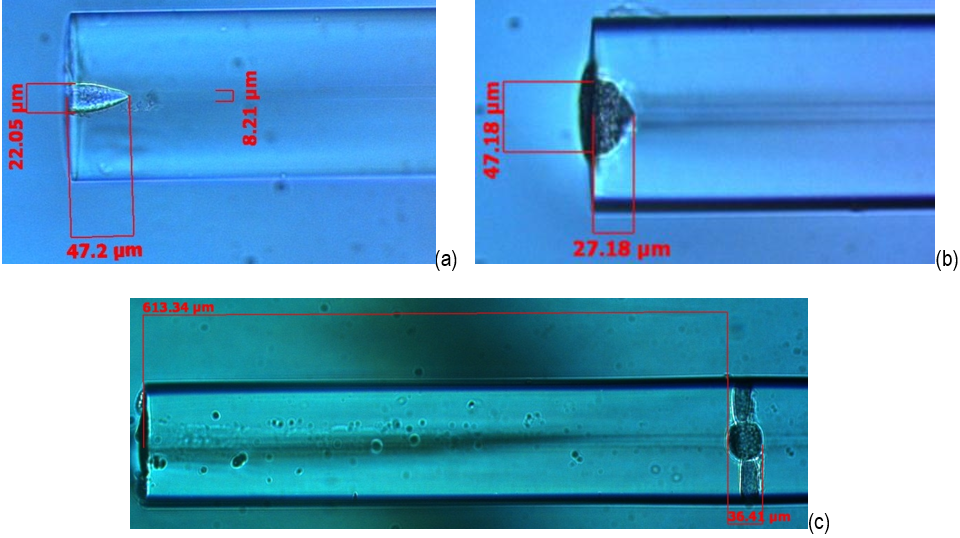
We also considered organic scintillators in existing doped POF. Two different designs of BCF10 joined to PMMA fibre were considered, the first was based on a simple butt-coupling with tube and the second was a “Plug and Play” design for the rapid and effective assembly of radiation sensors, as illustrated in Fig. 5.1.3. The butt-coupled fibres were flat cleaved and joined to realize a BCF-10:PMMA fibre sensor. However, this simple design has a final diameter that exceeds the fibres diameter, >1mm, which does not meet our design criteria, Fig. 5.1.3(a). Therefore, to reduce the outer sensor diameter, without compromising sensor robustness, we employed fsL processing of the fibres. In a 5-mm fibre length of BCF-10, the fsL selectively removed fibre cladding until a central cylindrical protrusion was realized (“male” joint). The 1-m length of PMMA fibre underwent core/cladding removal at one end to produce a cylindrical hollow (a “female” joint). The outer and inner dimensions of the cylindrical protrusion and hollow were precisely micro-machined to enable a coupling joint to be made when the fibres were pressed together, hence the reference to a “Plug and Play” architecture (Fig. 5.1.3(b)). A small amount of UV curing was used to seal the joint and the outer diameter was reduced to only 1 mm, which is ideal for dosimetry applications. The Plug and Play design is as good as the other butt-coupling design, with the advantage that the overall sensor dimensions remain small (WP6).
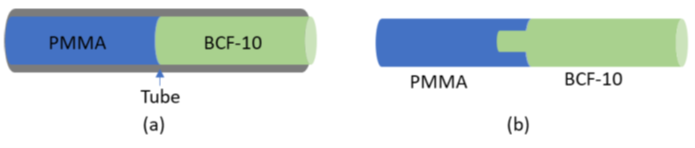
Task 5.3: To research the inscription of FBGs in silica fibres using the femtosecond laser.
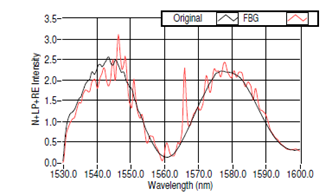
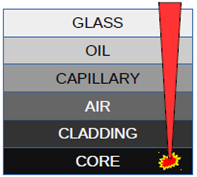
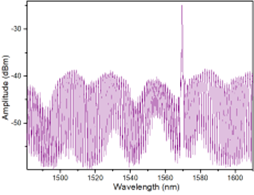
Fig. 5.3.1: (a) Typical measured FP spectrum after the FBG integration (UL design), (b) Note that the UL sensor requires focussing through five layers of material to reach the fibre core for FBG inscription, (c) FP/FBG spectrum (CUT design).
Task 5.4: Laser etching of the sensor end face
Laser etching (micromachining) the end face of the oxygen sensor is a unique alternative to acid-based wet-etch techniques for glass modification. The flexibility afforded by this method allows for selective etching (micromachining) any region of the end face. CUT led Task 5.3 in close collaboration with UL. In the figure below are presented the first attempts of laser etching the end face and the recorded spectrum of the FP interferometer, where we actually record laser pressure during the inscription. Note that as we moved away from the UL FP design, the role of end face micromachining changed significantly. There was no longer a need for laser etching of the end cap.
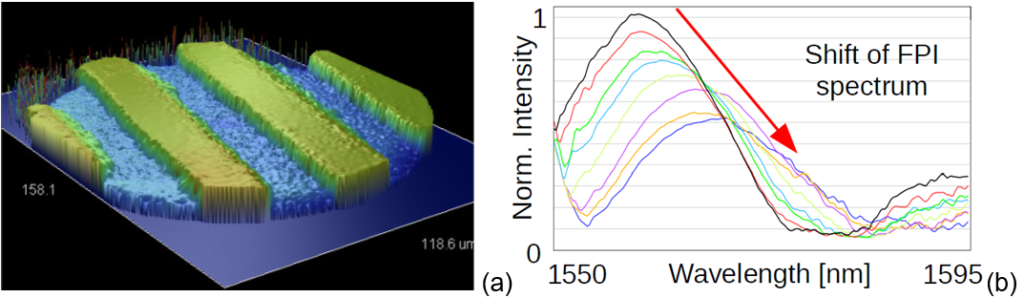
Task 5.5: Femtosecond laser surface structuring – self-cleaning surfaces
Table 5.1: Pattern for different micro pit radii and its direct captured image from the side with droplet deposition for glass slide.
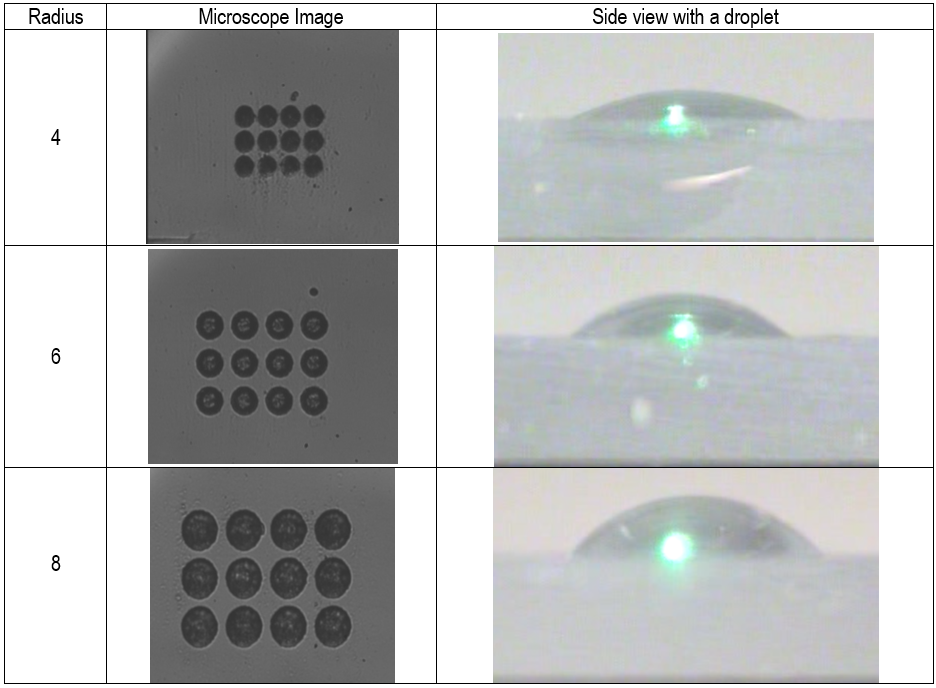